Sn96.5Ag3Cu0.5 Stick SAC305 Lead Free Solder Bar for Wave soldering
Sn96.5Ag3Cu0.5 Stick SAC305 Lead Free Solder Bar for Wave Soldering
As the world becomes more environmentally conscious, the use of lead-free solder has become increasingly popular in the electronics industry. Sn96.5Ag3Cu0.5 SAC305 is a lead-free solder alloy that has gained widespread acceptance due to its excellent properties and compatibility with a wide range of materials. It's a RoHS compliant solder, consisted of 96.5% of tin, 3% of silver and 0.5% of copper. In this article, we will introduce the Sn96.5Ag3Cu0.5 SAC305 solder bar, its features and benefits, and how to use it for wave soldering.
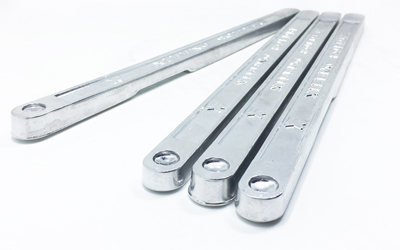
Product Features and Benefits of Sn96.5Ag3Cu0.5 Stick SAC305 Solder Bar for Wave Soldering:
The SAC305 solder bar (Sn96.5Ag3Cu0.5 stick bar) is a high-quality lead-free solder alloy that offers several benefits. It has a melting point of 217-220°C, which is lower than the melting point of traditional lead-based solders. This lower melting point reduces the risk of thermal damage to electronic components during the soldering process. The alloy also has excellent wetting properties, which allows it to flow smoothly and evenly over the surface of the joint, resulting in a strong and reliable bond.
Another benefit of the Sn96.5Ag3Cu0.5 SAC305 solder bar is its compatibility with a wide range of materials. It can be used to solder copper, brass, nickel, and other metals commonly used in the electronics industry. The alloy also has good resistance to thermal cycling and thermal shock, which makes it suitable for use in high-temperature applications.
And the silver content in this lead free solder bar adds up to the electrical conductivity and making the solder joint not easy to get fatigue during thermal circular (hot & cold environment).
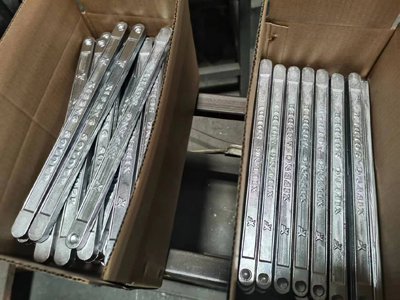
How to Use Sn96.5Ag3Cu0.5 Stick SAC305 Solder Bar for Wave Soldering
Wave soldering is a common method used in the electronics industry to solder through-hole components to printed circuit boards (PCBs). The process involves passing the PCB over a wave of molten solder, which wets the leads of the components and creates a permanent bond. By using wave soldereing technology along with solder stick bar, a high productivity of manufacutring can be easily achieved. Here are the steps to use Sn96.5Ag3Cu0.5 SAC305 solder bar for wave soldering:
1. Prepare the PCB: Before soldering, ensure that the PCB is clean and free from any contaminants that may affect the soldering process. This can be done by using a flux remover or cleaning solution.
2. Preheat the PCB: Preheating the PCB helps to reduce thermal shock and prevent damage to the components. The temperature should be set according to the specifications of the PCB and the components being soldered.
3. Apply flux: Apply a flux to the areas where the solder will be applied. This helps to remove any oxide layers and improve the wetting properties of the solder.
4. Load the solder bar: Load the Sn96.5Ag3Cu0.5 solder stick bar (SAC305 solder bar) into the wave soldering machine. The temperature should be set according to the melting point of the solder.
5. Solder the components: Pass the PCB over the wave of molten solder, ensuring that all the leads are wetted evenly. The solder should flow smoothly and create a strong bond.
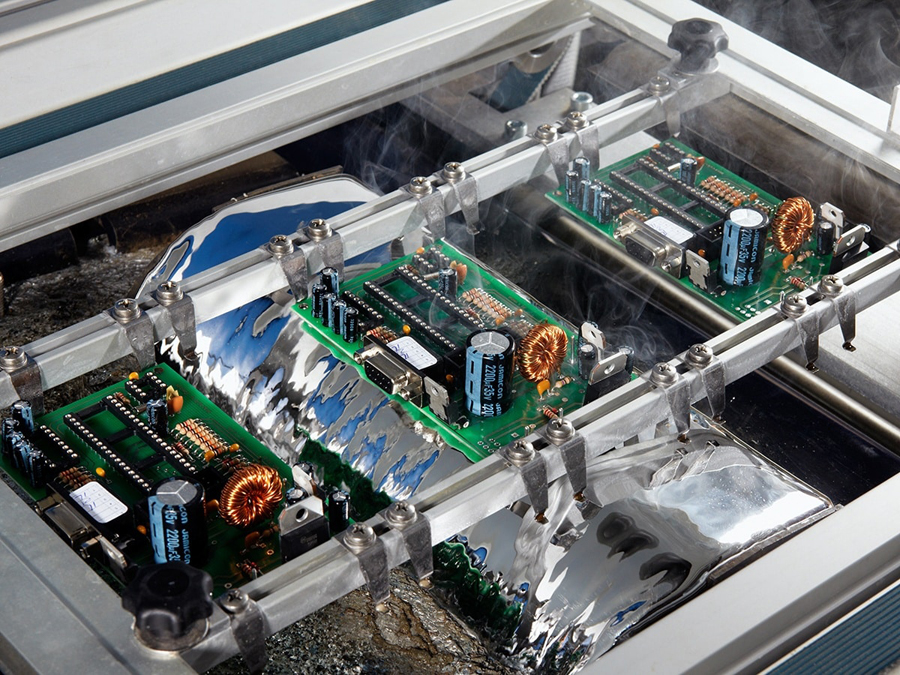
Conclusion
The Sn96.5Ag3Cu0.5 SAC305 solder bar is an excellent choice for wave soldering due to its low melting point, excellent wetting properties, and compatibility with a wide range of materials. By following the steps outlined in this article, you can achieve high-quality solder joints that are reliable and long-lasting. As the demand for lead-free solder continues to grow, Sn96.5Ag3Cu0.5 SAC305 is a reliable and effective solution for your soldering needs.
If you need to buy Sn96.5Ag3Cu0.5 Stick SAC305 Lead Free Solder Bar for Wave soldering from China, please contact our sales team. Email: xfsolder@gmail.com or xfsolder@163.com ; Whatsapp/Wechat: 0086 13450770997
Hits: 【Print】